About the Book

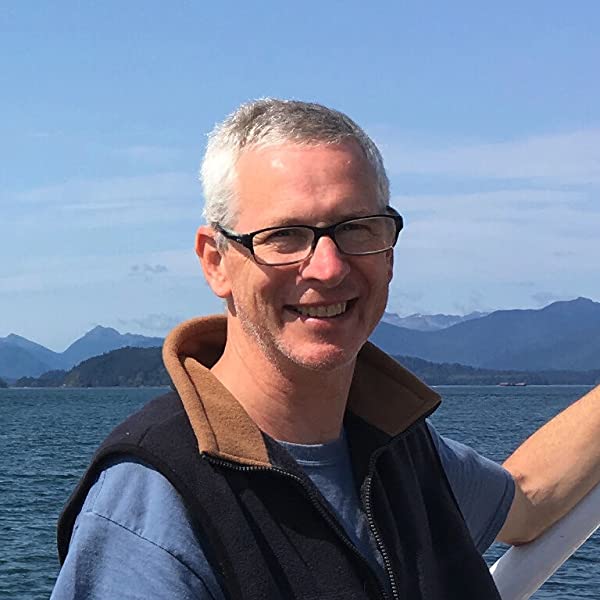
About the Author
Work should be good – people should go home feeling like they made a difference. That’s my starting point. One of the best ways to improve people’s work lives is to improve the skills of the leadership team. So, I help organizations achieve significant gains in performance and I achieve that by improving the skills of the management team. That makes for good work.
The results can be remarkable. In past projects where I’ve led the process, the team in a lab reduced its customer wait times by 45% in 12 weeks, the team in a factory reduced errors (remake and rework) by 85% in 5 months, and another factory team changed their procedures to produce 60% more product with the same equipment and people in 5 months.
By background, I’m an industrial engineer. I have run five manufacturing plants and several warehouses, and done consulting for over 15 years. I have done over 100 talks and presentations, and written over 100 published articles. I have taught at two universities and a college, including courses on lean thinking, project risk management, simulation, government policy, and strategy.